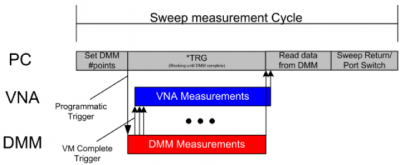
Voltage and Current Measurements with a VNA and DMM
April 20, 2018Background
Vector Network Analyzers (VNAs) are used to measure the reflection and transmission coefficients, or S-parameters, of a Device Under Test (DUT). When the DUT is passive, the VNA may be the only tool necessary. But some devices are active and require an external power source for operation. In such active applications, it may be useful to perform voltage or current measurements of the DUT as the VNA generator sweeps over frequency or power.
For example, characterization of a log amplifier may involve measurement of the detector’s output voltage synchronously with measurement of its S11 Return Loss. An amplifier manufacturer can simultaneously measure the gain and current draw of an amplifier DUT while the VNA sweeps its transmitter through various RF power levels and frequencies. Generally, the measured voltage and current will depend on the RF frequency, RF input power, and DUT temperature, each of which can be monitored and plotted against the supplied voltage or current.
There are several approaches to this challenge. Some VNAs incorporate a general-purpose analog voltage input port that measures voltages synchronously with the VNA sweep. This input port, sometimes named “Aux” (External Auxiliary Input), typically supports limited accuracy, voltage-only measurements over the range -10V to +10V. Alternatively, an independent Digital Multimeter (DMM) can be used to collect the voltage or current measurements as the VNA sweeps.
The latter approach, constructing a test setup with a VNA, software, and a DMM can be achieved with a PC-driven VNA from Copper Mountain Technologies. The instrument is suited for the application due to its programmability and trigger-on-point functionality, enabling highly accurate and quick synchronous voltage or current measurements by adding a simple program and an affordable, general purpose DMM.
Measurement Setup
In this demonstration, the CMT Full-Size 804/1 VNA interfaces with a Windows PC via USB1. Port 1 of the VNA connects to the amplifier input and Port 2 connects to the amplifier output. A BNC cable connects the “VM Complete” output of the DMM to the VNA’s External Trigger input. In this demonstration a BK Precision 1761 DC Power Supply delivers +12V DC to a Mini-Circuits ZX60-8008E-S+ Amplifier and a 34461A DMM measures the current draw and interfaces to the PC via USB.
The cycle shown in Figure 1 repeats until the DMM has completed all its measurements. In this way, the system quickly collects a large number of measurement points with a single, programmatically-issued trigger.
Figure 1: The sequence begins with a programmatic VISA trigger to the DMM. The DMM measures the DUT current, then generates a pulse on its VM Complete output. The VNA receives the pulse at its external trigger input, measures S-parameters, and readies its generator for the next point. Meanwhile the DMM waits for a delay time to pass before measuring the next current corresponding to the next VNA output conditions.
The stages and commands involved with the execution of each sweep are illustrated in Figure 2.
Figure 2: During each sweep cycle, the DMM is configured and then triggered. Measurements are collected without programmatic intervention until the sweep completes, at which point the DMM measurements are read and a delay is incurred to accommodate VNA port switching and generator return.
1 The automation program here was developed in MATLAB, but the VNA can be programmed in any environment with Microsoft COM support (examples are available for C++, Visual Basic in Excel, LabView, and MATLAB).
In this particular example, four sweep cycles are combined sequentially to achieve the full set of measurements as depicted in Figure 3.
Figure 3: During the first sweep cycle, Port 1 generates a Power Sweep signal while the VNA measures S11 and S21. Next, the generator switches to Port 2 and a reverse Power Sweep is performed, allowing the VNA to measure S22 and S12. Frequency Sweeps from Port 1 and Port 2 are the 3rd and 4th sweeps respectively.
Measurement Speed
In addition to the per-point measurement time of the VNA and DMM (approximately TVNA ≈100 µsec and TDMM ≈ 1 msec respectively) additional delays factor in the application. Those are:
- Tsetup ≈ 1.0 sec: Time required to initialize all settings of the DMM and VNA.
- Treturn ≈ 10 msec: VNA delay to prepare generator for next sweep.
- Tmargin ≈ 25 µsec: Per-point DMM delay for VNA measurement.
- TUSB ≈ 10 msec: USB latency associated with DMM or VNA interface.
- Tpost ≈ 100 msec: Post-processing time required to plot, save, or otherwise manipulate data following completion of the measurement cycle.
Neglecting the one-time setup, the overall cycle measurement time can be estimated as:
Ttotal ≈ (Nsweeps – 1) * (Treturn + TUSB) + Npoints * (TVNA + Tmargin + TDMM) + Tpost
Substituting the approximate values from above, the estimate reduces to:
Ttotal ≈ (Nsweeps – 1) * 20 msec + Npoints * 1.125 msec + 100 msec
Typically, the program spends the bulk of execution time waiting for the DMM to complete measurements. When DMM measurements are not required for every sweep, the time per point for those sweeps decreases significantly. In addition, power and frequency sweeps from Port 2 may be unnecessary since most amplifiers only function properly when the signal enters their input.
Typically, the program spends the bulk of execution time waiting for the DMM to complete measurements. When DMM measurements are not required for every sweep, the time per point for those sweeps decreases significantly. In addition, power and frequency sweeps from Port 2 may be unnecessary since most amplifiers only function properly when the signal enters their input.
Maximizing Measurement Speed
The measurement speed of the DMM can be a limiting factor, since at 1,000 points per second, the DMM consumes the bulk of the measurement time. In order to significantly speed the process, using a faster (but typically more expensive) DMM—models that can collect up to 10,000 or 50,000 pts/sec are readily available. This application provides a solution while using a lower cost DMM. Regardless of the DMM chosen, to maximize the speed of the DMM measurement, one should manually set the measurement range to the smallest setting compatible with the DUT, select a small aperture, and disable Auto Zero.
To optimize the VNA’s speed, IF Bandwidth should be set to the maximum value consistent with the application’s necessary dynamic range. For amplifier characterization, 30 kHz IF bandwidth is typically more than adequate, allowing the VNA to complete measurements at its specified 100 µsec/point.
Results
Any of the four measurement cycles in Figure 3 can optionally be omitted, or can be performed without synchronous DMM current measurements, according to the specific requirements of the application. Measurement speeds were determined for each of 4 different scenarios (named M1, M2, M3, and M4):
The table below compares the predicted measurement time, according to the formulas in the preceding section, with empirically determined measurement times based on 100 iterations.
Conclusion
While an instrument with a built-in voltage measurement provides convenience, using a separate DMM and a VNA provides a more flexible test setup, which can be configured for higher accuracy and specific features needed for the application. A CMT analyzer pairs well with any programmable, off-the-shelf DMM and offers an optimal and cost-effective solution for making voltage and current measurements.