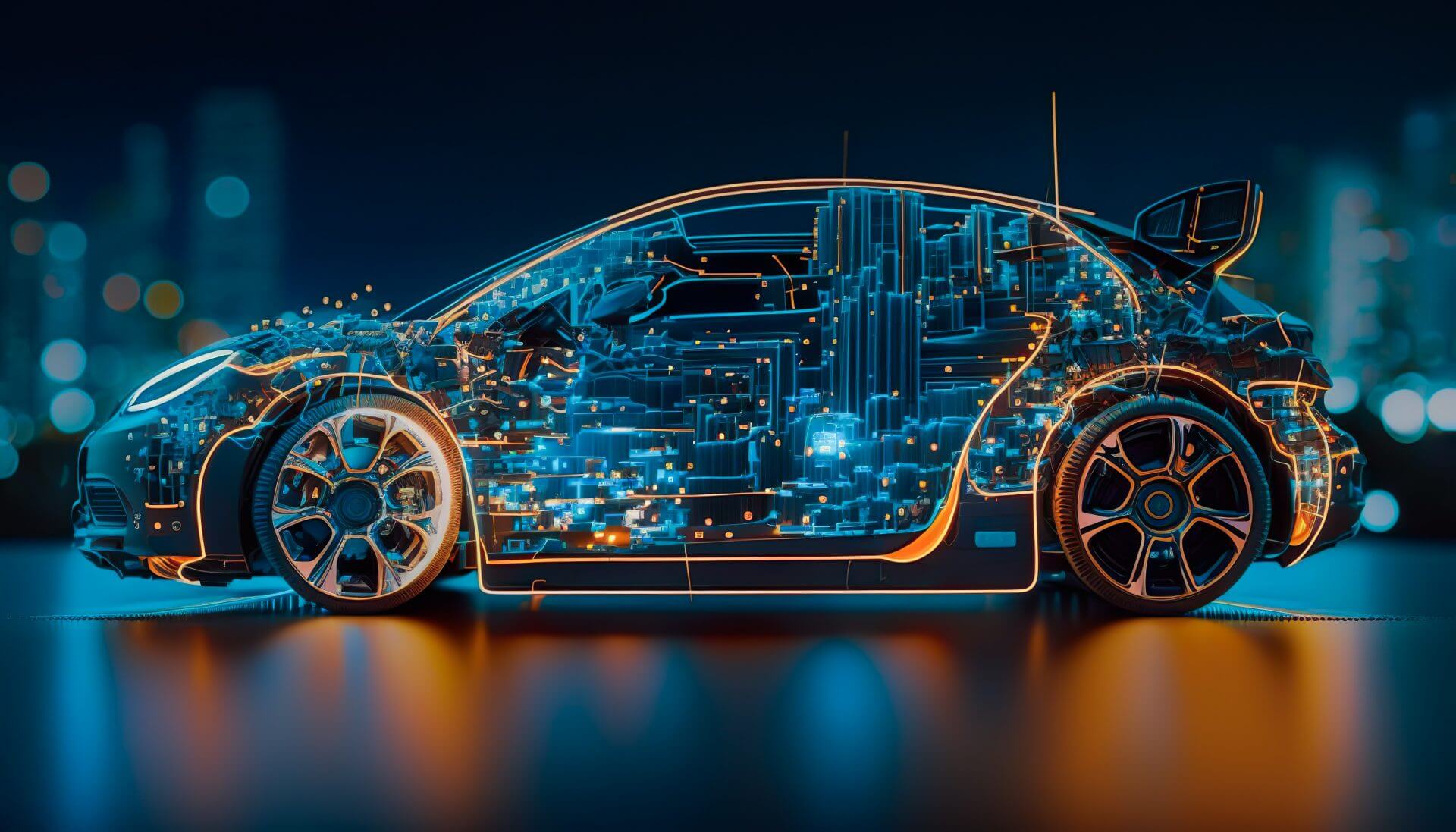
Understanding Shielding Effectiveness
November 20, 2023Introduction
Shielding, or screening effectiveness, is essential to the safe operation of electric vehicles (EVs). There was a time when the noise generated by the spark plugs firing in an internal combustion engine caused an annoying buzz when listening to the AM radio. Circuit designs have since evolved, and this issue was eventually resolved, but now the issue is back. To drive the electric motors, EVs are switching over a hundred amps at 500 to 900 VDC at perhaps a 10 to 20 kHz rate. Here, the potential interference is more than an annoyance, it can affect the Automatic Driver Assistance Systems (ADAS) or other critical systems, which affects the safety of both the driver and the passengers. Controlling interference is therefore a critical requirement and understanding the shielding effectiveness of the transmission lines carrying power and data is essential to mitigating it.
Coaxial Cables
A coaxial cable passes RF current on both the inner conductor and the inside of the shield. The RF current on the inside of the shield is the return current flowing in the opposite direction and balances that of the inner conductor. No RF current should flow on the outside of the shield, as shown in Figure 1. Because of this balance, there should be no radiated RF energy. In practice, the shield is not perfect and may have gaps in the braid, and some RF current penetrates due to skin effect. Shielding effectiveness measurements are meant to determine the amount of this RF leakage.
Figure 1 – Coaxial Current Flow
The DC Drive Cables
The cables carrying the motor drive are the most significant contributor to this effect, and so should be carefully selected. A typical cable—Kromberg & Schubert PN 64997451 for instance—has a stranded copper core with 12.5 mm (0.49”) diameter covered by 0.8 mm of silicone insulation, followed by 0.2 mm of tinned copper braid covered with an aluminum foil. Finally, the braid is covered with 0.9 mm of silicone insulation for a total cable diameter of about 18 mm (0.71”). This is a particularly large cable, meant for high motor drive currents.
At frequencies up to 100 MHz, the characteristic impedance of this cable might be close to 2Ω, and smaller cables might range as high as 10 ohms. The shielding of such a cable is characterized in two ways. For lower frequencies—up to 100 MHz—where there is little change in phase along the length of the cable, the transfer impedance is evaluated, which is essentially a DC property. Above 30 MHz, the screening effectiveness may be evaluated to several GHz.
These cables are not designed to be RF coaxial cables, and as such, have a low cut-off frequency, where the TE11 waveguide mode can be active along with the desired TEM mode. Interference between the two modes due to differing velocity factors causes ripples in the frequency response which would find its way into a screening effectiveness measurement. The TE11 mode for a coaxial cable begins at:
Where the D terms are the diameters of the inner and outer conductors in meters, c is the speed of light in m/s, and µ and ε are the relative magnetic and dielectric constants of the insulating materials. For the Kromberg cable example above, fc is 4 GHz.
Let’s look at these two measurements in the following sections.
Transfer Impedance
The transfer impedance measurement is defined by IEC62153-4-3(Ed 2.0). A tri-axial fixture may be used to measure a Cable Under Test (CUT).
Figure 2 – Transfer Impedance Measurement
The transfer impedance is defined as the ratio of the longitudinal voltage developed on the shield of a CUT due to a current applied to its center conductor per unit length. At DC, this is equal to the resistance per unit length of the shield. Figure 2 shows the schematic of a tri-axial fixture to make this measurement. The tri-axial fixture has good high-frequency response and low susceptibility to external interference, but a ground-plane fixture may also be used.
For this fixture, the CUT is suspended above a ground-plane plate. The far end of the CUT may be shorted or terminated in its own characteristic impedance, Z1. Source impedance Z0 may be matched to the CUT characteristic impedance Z1 with restive matching network ZM1 and ZM2. The signal on the shield will be picked off the far end with series termination Z2 which matches the characteristic impedance of the shield/ground-plane combination.
Figure 3 – Ground Plane Fixture
Figure 3 shows the schematic for a ground plane fixture. Z0 is the impedance of the source, usually 50 ohms. Z1 is the characteristic impedance of the CUT and Z2 is the free-wire impedance of the shield to the ground plane beneath it. The transimpedance calculation is somewhat more complicated due to the matching resistors but is still V2 of the shield divided by I1 of the center conductor current per unit length.
For large distances, h between the shield and the ground plane compared to the diameter of the shield, Z2 is given by:
Where h is the height of the CUT above the ground plane and d is the diameter of the shield. Matching resistors Z1 and Z2 improve the frequency response of the fixture.
Shielding Effectiveness
The transfer impedance measurement is defined by IEC62153-4-4(Ed 2.0). Above 100 MHz or so, there will be more phase shift along the length of a cable and there is the potential for interference due to electromagnetic radiation (EMI). The radiation condition requires a conductor long enough or a frequency high enough to produce a significant phase shift from one end to the other, creating the tangential electric field component needed to generate a radiated electromagnetic wave. Shielding effectiveness applies to a cable which is greater than ten wavelengths long, or where guide velocity in the cable
and εr is the cable dielectric constant.
For common silicone insulation, with a dielectric constant of 3.5, a one-meter length is ten wavelengths at 1.6 GHz. Two meters for 800 MHz and so on.
Effective shielding can reduce EMI from a cable. The screening attenuation, expressed as a positive number, is defined by the ratio of peak radiated power Pr,max from the CUT generated by peak voltages on the screen to the input power P1:
Screening attenuation is measured in a tri-axial fixture, as in Figure 4 below.
Figure 4 – Triaxial Screening Effectiveness Measurement
The input matching circuit is a pair of resistors, a series followed by a shunt value to match the 50Ω source impedance, Zg of the Vector Network Analyzer (VNA) to the 1 to 10Ω characteristic impedance, Z1 of the CUT. The series resistor, Rs and shunt resistor, Rp may be calculated as follows:
The excess loss due to the resistive matching resistors is:
for 50Ω Zg to 9Ω Z1 this is -20.5 zdB.
Terminating resistor R1 must equal the characteristic impedance of the CUT. Damping resistor R2 is required to dissipate oscillations of the inner structure which at some point will be a quarter wavelength resonator, grounded on the left-hand side. A 50Ω resistor would be prudent when the output is fed to a 50Ω VNA input. This resistor would produce another 6 dB of loss.
For our case of a CUT with 9Ω characteristic impedance, matching series resistor 45.3Ω, shunt resistor 10Ω, and a 50Ω damping resistor, the screening effectiveness may be measured directly by a VNA S21 measurement compensated by adding 26.5 dB to the result.
Determining the Characteristic Impedance of the CUT
There are two simple ways to determine the characteristic impedance, Z1 of the CUT. First, a sample of the cable should be cut to an eighth of a wavelength at some chosen test frequency, Ftest.
Where L is the cut length in meters, c is speed of light in m/s, and ε1 is the dielectric constant of the cable.
Measure the impedance of the cable from one end with the other end open, Zopen. Short the open end and measure again, Zshort. Then:
In a similar method, cut the cable a little over a quarter wavelength long at a test frequency, Ftest—which is a little over 40mm long for silicone dielectric with εr = 3.5 at 1 GHz. Terminate one end with 50Ω—perhaps using four 200Ω resistors—and observe the response using the Smith chart display on a VNA, as shown in Figure 5. Starting from a very low frequency to Ftest, the response will describe a clockwise circle starting at 50Ω and eventually crossing the real axis at some low value, R. Find this crossing point and compute:
Figure 5 – Smith Chart Measurement of Z1
For our 9Ω example, we have .
Conclusion
Two important cable measurements have been shown; Transfer impedance and shielding effectiveness. Both have broad implications for the automotive industry. As electronic systems continue to evolve, it is imperative that critical subsystems do not interfere with each other, particularly those that involve driver safety. A basic understanding of these measurements is important, and Copper Mountain Technologies furnishes Vector Network Analyzers to make them and meet the needs of the industry. Please feel free to visit our website at www.coppermountaintech.com to see our world-class products and avail yourself of the educational materials in our technical library, videos, and webinars.